Destylarki rozpuszczalników odgrywają kluczową rolę w wielu gałęziach przemysłu, a ich zastosowanie jest niezwykle szerokie. W przemyśle chemicznym destylacja jest podstawowym procesem, który pozwala na oczyszczanie i separację różnych substancji chemicznych. Dzięki wykorzystaniu destylarek możliwe jest uzyskanie wysokiej czystości rozpuszczalników, co jest niezbędne do produkcji wielu chemikaliów, farb, lakierów oraz farmaceutyków. W branży petrochemicznej destylacja służy do oddzielania frakcji ropy naftowej, co umożliwia produkcję paliw oraz innych produktów naftowych. W przemyśle spożywczym destylarki wykorzystywane są do produkcji alkoholi oraz ekstraktów smakowych, gdzie kluczowe jest zachowanie odpowiednich właściwości organoleptycznych. Ponadto w laboratoriach badawczych i analitycznych destylacja jest niezbędna do oczyszczania reagentów oraz próbek, co ma istotne znaczenie dla uzyskiwania wiarygodnych wyników badań.
Jakie są korzyści z używania destylarek rozpuszczalników
Używanie destylarek rozpuszczalników przynosi wiele korzyści zarówno dla producentów, jak i dla środowiska. Przede wszystkim dzięki procesowi destylacji można uzyskać wysokiej jakości produkty o dużej czystości, co jest kluczowe w wielu branżach. W przypadku przemysłu chemicznego czystość surowców ma bezpośredni wpływ na jakość finalnych produktów, dlatego inwestycja w nowoczesne destylarki staje się niezbędna. Kolejną korzyścią jest możliwość recyklingu rozpuszczalników, co pozwala na oszczędność surowców oraz redukcję odpadów. Dzięki temu przedsiębiorstwa mogą zmniejszyć swoje koszty operacyjne oraz przyczynić się do ochrony środowiska naturalnego. Dodatkowo nowoczesne destylarki charakteryzują się wysoką efektywnością energetyczną, co przekłada się na niższe zużycie energii podczas procesu destylacji. Warto również zauważyć, że automatyzacja procesów związanych z destylacją zwiększa bezpieczeństwo pracy oraz minimalizuje ryzyko błędów ludzkich.
Jakie są najnowsze technologie w dziedzinie destylacji
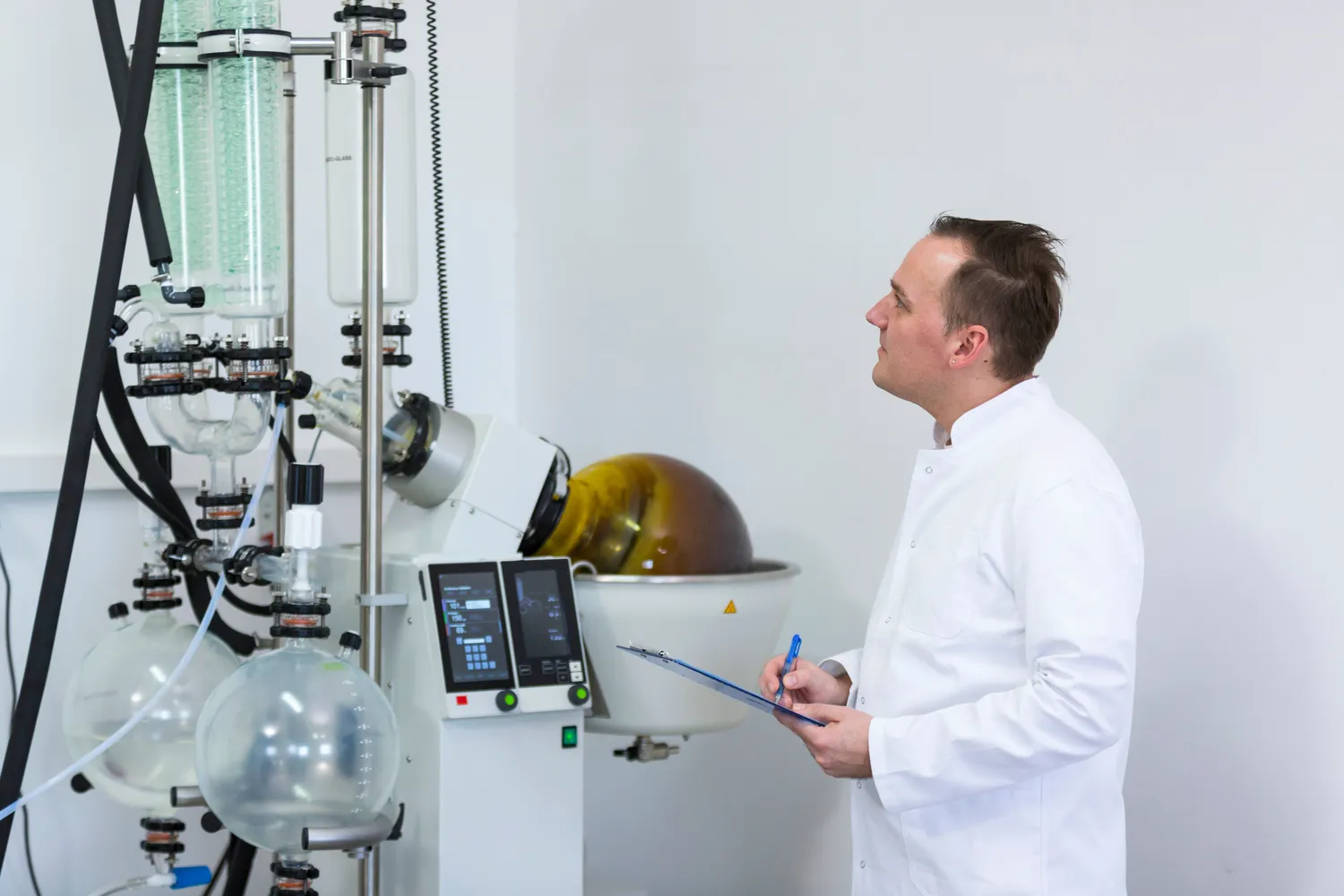
W ostatnich latach technologia związana z destylacją rozwinęła się znacząco, co wpłynęło na efektywność i wydajność procesów przemysłowych. Nowoczesne destylarki wyposażone są w zaawansowane systemy sterowania, które umożliwiają precyzyjne monitorowanie parametrów procesu w czasie rzeczywistym. Dzięki temu operatorzy mogą szybko reagować na wszelkie zmiany i dostosowywać warunki pracy urządzenia do aktualnych potrzeb produkcyjnych. Ponadto rozwój technologii membranowych i kriogenicznych otworzył nowe możliwości w zakresie separacji substancji chemicznych. Te innowacyjne metody często oferują wyższą efektywność energetyczną oraz mniejsze zużycie rozpuszczalników niż tradycyjne metody destylacji. Również zastosowanie nanotechnologii w budowie elementów destylacyjnych pozwala na zwiększenie powierzchni kontaktu między fazami, co przyspiesza proces separacji. Warto także wspomnieć o rosnącym zainteresowaniu ekologicznymi rozwiązaniami, takimi jak wykorzystanie energii słonecznej czy geotermalnej do zasilania procesów destylacyjnych.
Jakie są wyzwania związane z użytkowaniem destylarek
Mimo licznych korzyści płynących z użytkowania destylarek rozpuszczalników, istnieje także szereg wyzwań, które przedsiębiorstwa muszą stawić czoła. Jednym z głównych problemów jest konieczność regularnej konserwacji i serwisowania urządzeń, aby zapewnić ich prawidłowe działanie i długowieczność. Niewłaściwe utrzymanie może prowadzić do awarii sprzętu oraz strat finansowych związanych z przestojami produkcyjnymi. Kolejnym wyzwaniem jest zarządzanie odpadami powstającymi podczas procesu destylacji, które mogą być szkodliwe dla środowiska. Firmy muszą przestrzegać rygorystycznych norm dotyczących utylizacji tych odpadów oraz inwestować w technologie minimalizujące ich powstawanie. Dodatkowo zmieniające się przepisy prawne dotyczące ochrony środowiska mogą wymuszać na przedsiębiorstwach dostosowywanie swoich procesów produkcyjnych do nowych regulacji, co wiąże się z dodatkowymi kosztami i koniecznością szkoleń pracowników.
Jakie są różnice między destylacją prostą a frakcyjną
Destylacja jest procesem, który można podzielić na różne metody, a dwie z najczęściej stosowanych to destylacja prosta i frakcyjna. Destylacja prosta jest najstarszą i najprostszą formą tego procesu, polegającą na podgrzewaniu cieczy do momentu, w którym zaczyna parować, a następnie skraplaniu powstałych oparów. Ta metoda jest skuteczna w przypadku substancji o znacznej różnicy temperatur wrzenia, co pozwala na ich efektywne oddzielenie. Z kolei destylacja frakcyjna jest bardziej złożonym procesem, który wykorzystuje kolumny destylacyjne do separacji mieszanin cieczy o zbliżonych temperaturach wrzenia. W tej metodzie para przechodzi przez kolumnę, gdzie wielokrotnie skrapla się i paruje, co pozwala na uzyskanie wyższej czystości produktów końcowych. Destylacja frakcyjna jest szczególnie przydatna w przemyśle petrochemicznym, gdzie konieczne jest oddzielenie różnych frakcji ropy naftowej. Wybór odpowiedniej metody destylacji zależy od specyfiki procesu produkcyjnego oraz rodzaju substancji, które mają być oddzielone.
Jakie są kluczowe komponenty destylarek rozpuszczalników
Destylarki rozpuszczalników składają się z kilku kluczowych komponentów, które współpracują ze sobą w celu efektywnego przeprowadzenia procesu destylacji. Podstawowym elementem jest zbiornik do podgrzewania cieczy, który może być wyposażony w różne źródła ciepła, takie jak elektryczność czy para wodna. Ważnym komponentem jest także kolumna destylacyjna, która umożliwia wielokrotne skraplanie i parowanie cieczy, co zwiększa efektywność separacji. W górnej części kolumny znajduje się skraplacz, który chłodzi pary i przekształca je z powrotem w ciecz. Oprócz tych podstawowych elementów destylarki często wyposażone są w systemy monitorowania i kontroli temperatury oraz ciśnienia, co pozwala na precyzyjne zarządzanie procesem. Dodatkowo niektóre nowoczesne urządzenia mogą mieć zastosowane technologie automatyzacji, które zwiększają wydajność i bezpieczeństwo pracy. Kluczowe jest również odpowiednie zaprojektowanie układu rur i zaworów, które umożliwiają sprawny przepływ substancji oraz minimalizują straty materiałowe.
Jakie są regulacje prawne dotyczące destylacji rozpuszczalników
Regulacje prawne dotyczące destylacji rozpuszczalników są niezwykle istotne dla przedsiębiorstw zajmujących się tym procesem, ponieważ wpływają na sposób prowadzenia działalności oraz na ochronę środowiska. W wielu krajach istnieją szczegółowe przepisy dotyczące emisji substancji szkodliwych do atmosfery oraz wymagań dotyczących utylizacji odpadów powstających podczas procesu destylacji. Firmy muszą przestrzegać norm określonych przez organy regulacyjne, takie jak Ministerstwo Środowiska czy lokalne agencje ochrony środowiska. W przypadku nieprzestrzegania tych przepisów przedsiębiorstwa mogą zostać ukarane grzywnami lub zmuszone do wprowadzenia kosztownych zmian w swoich procesach produkcyjnych. Ponadto regulacje te często wymagają przeprowadzania regularnych audytów oraz raportowania wyników dotyczących emisji i zużycia surowców. Warto również zauważyć, że przepisy te mogą się różnić w zależności od regionu geograficznego oraz rodzaju produkcji, co sprawia, że przedsiębiorstwa muszą być dobrze poinformowane o obowiązujących normach w swoim obszarze działalności.
Jakie są przyszłe kierunki rozwoju technologii destylacji
Przyszłość technologii destylacji zapowiada się obiecująco dzięki ciągłemu rozwojowi innowacyjnych rozwiązań oraz rosnącemu zainteresowaniu ekologicznymi metodami produkcji. Jednym z kluczowych kierunków rozwoju jest automatyzacja procesów destylacyjnych, która ma na celu zwiększenie efektywności oraz bezpieczeństwa pracy. Nowoczesne systemy sterowania umożliwiają precyzyjne monitorowanie parametrów procesu oraz szybką reakcję na wszelkie zmiany, co przekłada się na lepszą jakość produktów końcowych. Kolejnym ważnym trendem jest wykorzystanie technologii membranowych oraz kriogenicznych jako alternatywy dla tradycyjnej destylacji. Te nowoczesne metody oferują wyższą efektywność energetyczną oraz mniejsze zużycie surowców, co ma istotne znaczenie w kontekście ochrony środowiska. Również rozwój nanotechnologii otwiera nowe możliwości w zakresie budowy elementów destylacyjnych, co może przyczynić się do poprawy wydajności procesów separacyjnych. Warto także zwrócić uwagę na rosnące znaczenie recyklingu rozpuszczalników oraz poszukiwanie ekologicznych alternatyw dla tradycyjnych chemikaliów używanych w procesach przemysłowych.
Jakie są najlepsze praktyki w obsłudze destylarek
Aby zapewnić prawidłowe funkcjonowanie destylarek rozpuszczalników oraz maksymalizować ich wydajność, ważne jest przestrzeganie najlepszych praktyk związanych z ich obsługą i konserwacją. Przede wszystkim operatorzy powinni być dobrze przeszkoleni w zakresie obsługi urządzeń oraz znajomości zasad bezpieczeństwa pracy. Regularne kontrole stanu technicznego sprzętu są niezbędne do wykrywania potencjalnych usterek zanim staną się one poważnym problemem. Ważnym aspektem jest także dbanie o czystość elementów destylacyjnych oraz systemu rur, aby uniknąć kontaminacji produktów końcowych. Należy również regularnie kalibrować urządzenia pomiarowe używane do monitorowania temperatury i ciśnienia w procesie destylacji, aby zapewnić ich dokładność i wiarygodność wyników. Oprócz tego istotne jest przestrzeganie procedur dotyczących utylizacji odpadów powstających podczas procesu destylacji zgodnie z obowiązującymi przepisami prawnymi.