Destylator do rozpuszczalników to urządzenie, które wykorzystuje proces destylacji do oddzielania różnych substancji chemicznych. W praktyce oznacza to, że destylator podgrzewa ciecz, co powoduje jej parowanie, a następnie schładza pary, aby skropliły się z powrotem w ciecz. Proces ten jest niezwykle efektywny, ponieważ różne substancje mają różne temperatury wrzenia, co pozwala na ich selektywne oddzielanie. W przypadku rozpuszczalników, takich jak etanol czy aceton, destylacja jest kluczowym procesem w laboratoriach chemicznych oraz w przemyśle. Umożliwia ona uzyskanie czystych substancji, które mogą być używane w różnych aplikacjach, od produkcji farb po przemysł farmaceutyczny. Warto zaznaczyć, że skuteczność destylatora zależy od jego konstrukcji oraz zastosowanych materiałów. Współczesne destylatory często są wyposażone w dodatkowe elementy, takie jak kolumny rektyfikacyjne, które zwiększają wydajność procesu i pozwalają na uzyskanie wyższej czystości końcowego produktu.
Jakie są rodzaje destylatorów do rozpuszczalników
Na rynku dostępnych jest wiele rodzajów destylatorów do rozpuszczalników, które różnią się zarówno budową, jak i przeznaczeniem. Najpopularniejsze z nich to destylatory prostokątne oraz kolumnowe. Destylatory prostokątne są najczęściej stosowane w małych laboratoriach oraz w domowych warunkach, gdzie nie ma potrzeby przetwarzania dużych ilości substancji. Charakteryzują się prostą konstrukcją i łatwością obsługi. Z kolei destylatory kolumnowe są bardziej zaawansowane technologicznie i przeznaczone do przemysłowego użytku. Dzięki zastosowaniu kolumny rektyfikacyjnej umożliwiają one wielokrotne oddzielanie substancji, co prowadzi do uzyskania bardzo czystych produktów. Inne typy destylatorów obejmują destylatory próżniowe, które działają w obniżonym ciśnieniu i pozwalają na destylację substancji o wysokich temperaturach wrzenia bez ich degradacji. Wybór odpowiedniego typu destylatora zależy od specyfiki pracy oraz wymagań dotyczących czystości końcowego produktu.
Jakie zastosowania mają destylatory do rozpuszczalników
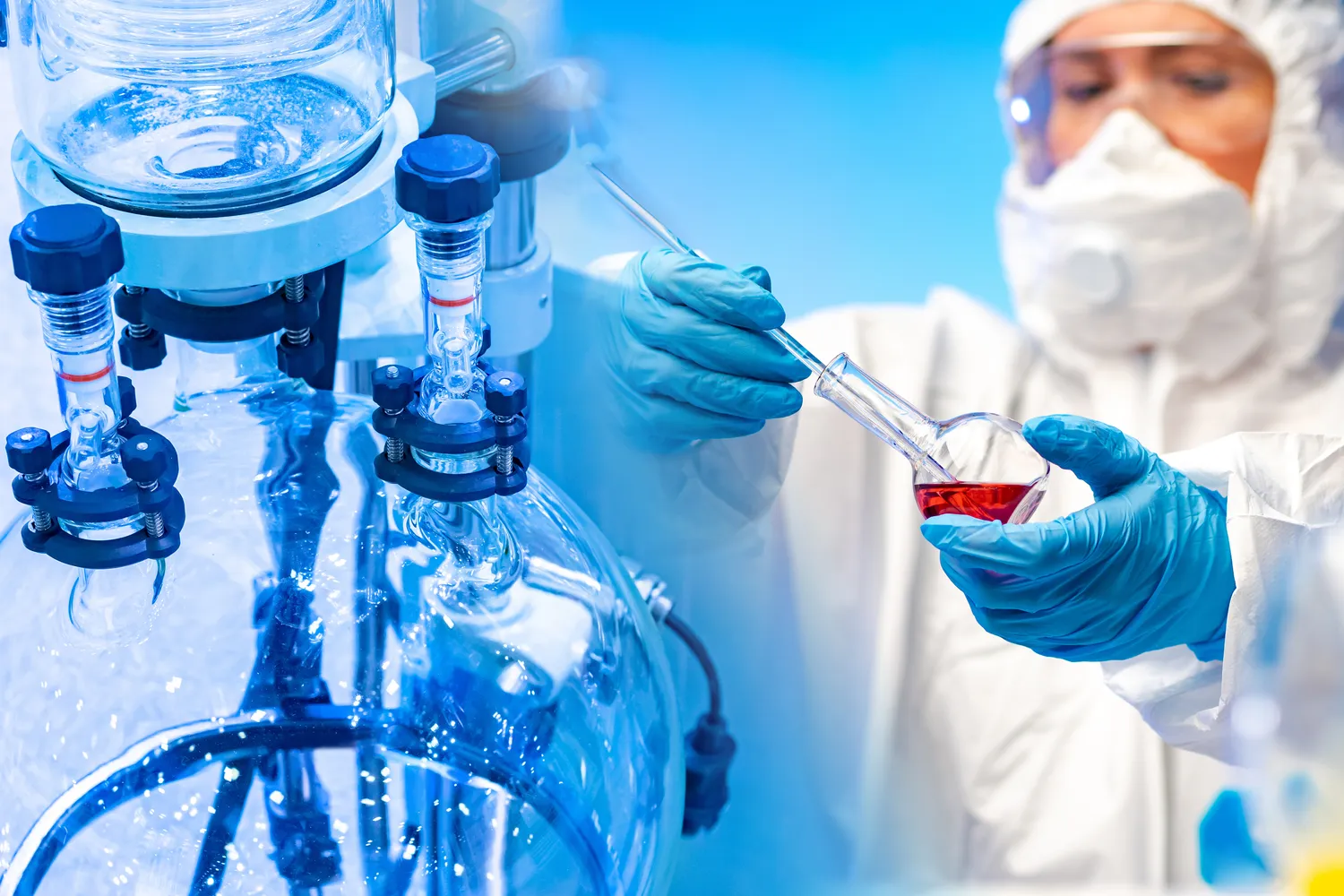
Destylatory do rozpuszczalników znajdują szerokie zastosowanie w różnych dziedzinach przemysłu oraz nauki. W laboratoriach chemicznych są wykorzystywane do oczyszczania substancji chemicznych oraz do przygotowywania roztworów o określonych stężeniach. Dzięki możliwości separacji składników mieszanin chemicznych, laboratoria mogą uzyskać czyste substancje potrzebne do dalszych badań lub eksperymentów. W przemyśle farmaceutycznym destylatory odgrywają kluczową rolę w produkcji leków, gdzie czystość składników jest niezwykle istotna dla bezpieczeństwa pacjentów. Ponadto destylatory są również wykorzystywane w przemyśle kosmetycznym do produkcji perfum oraz innych produktów pielęgnacyjnych. W branży spożywczej służą do produkcji alkoholi oraz ekstraktów roślinnych. Oprócz tego coraz częściej stosowane są w procesach recyklingu rozpuszczalników, co przyczynia się do ochrony środowiska poprzez zmniejszenie ilości odpadów chemicznych.
Jakie materiały są używane w budowie destylatorów
Budowa destylatorów do rozpuszczalników opiera się na zastosowaniu różnych materiałów, które muszą spełniać określone wymagania dotyczące odporności chemicznej oraz termicznej. Najczęściej wykorzystywanym materiałem jest stal nierdzewna, która charakteryzuje się wysoką odpornością na korozję oraz trwałością. Stal nierdzewna jest idealna do kontaktu z wieloma substancjami chemicznymi i zapewnia długotrwałe użytkowanie urządzenia. Innym popularnym materiałem jest szkło borokrzemowe, które jest stosowane głównie w laboratoriach ze względu na swoją odporność na wysokie temperatury i działanie agresywnych chemikaliów. Szkło pozwala również na łatwe monitorowanie procesu destylacji dzięki przezroczystości materiału. W niektórych przypadkach stosuje się także tworzywa sztuczne o wysokiej odporności chemicznej, które mogą być używane w mniej wymagających aplikacjach. Ważnym aspektem przy wyborze materiałów jest również ich łatwość w czyszczeniu oraz konserwacji, co ma kluczowe znaczenie dla zachowania wysokiej jakości procesów destylacyjnych.
Jakie są kluczowe elementy destylatora do rozpuszczalników
Kluczowe elementy destylatora do rozpuszczalników mają istotny wpływ na jego funkcjonalność oraz efektywność procesu destylacji. Podstawowym komponentem jest zbiornik, w którym odbywa się podgrzewanie cieczy. Zbiornik ten musi być wykonany z materiałów odpornych na wysoką temperaturę oraz działanie chemikaliów. Kolejnym istotnym elementem jest system grzewczy, który może być oparty na różnych technologiach, takich jak grzałki elektryczne czy palniki gazowe. Wybór odpowiedniego systemu grzewczego zależy od rodzaju rozpuszczalnika oraz wymagań dotyczących szybkości destylacji. Po parowaniu cieczy, opary przechodzą przez chłodnicę, gdzie następuje ich skraplanie. Chłodnica jest kluczowym elementem, który musi być odpowiednio dobrany do rodzaju substancji oraz warunków pracy. Dodatkowo, w bardziej zaawansowanych destylatorach można znaleźć kolumny rektyfikacyjne, które umożliwiają wielokrotne oddzielanie składników, co zwiększa czystość końcowego produktu. Oprócz tych podstawowych elementów, nowoczesne destylatory mogą być wyposażone w różnego rodzaju czujniki i automatyzację, co ułatwia kontrolowanie procesu i zwiększa bezpieczeństwo pracy.
Jakie są zalety korzystania z destylatorów do rozpuszczalników
Korzystanie z destylatorów do rozpuszczalników niesie ze sobą wiele korzyści zarówno dla przemysłu, jak i dla laboratoriów. Przede wszystkim pozwala na uzyskanie wysokiej czystości produktów chemicznych, co jest kluczowe w wielu aplikacjach, takich jak farmacja czy kosmetyki. Dzięki procesowi destylacji można skutecznie oddzielić niepożądane zanieczyszczenia oraz inne składniki, które mogą wpływać na jakość końcowego produktu. Kolejną zaletą jest możliwość recyklingu rozpuszczalników, co przyczynia się do zmniejszenia ilości odpadów chemicznych i ochrony środowiska. Wiele nowoczesnych destylatorów jest zaprojektowanych tak, aby minimalizować straty materiałowe i maksymalizować efektywność energetyczną. Dodatkowo, proces destylacji jest stosunkowo prosty i może być łatwo zautomatyzowany, co pozwala na oszczędność czasu oraz zasobów ludzkich. Warto również zauważyć, że dzięki różnorodności dostępnych modeli destylatorów można je dostosować do specyficznych potrzeb użytkowników, co sprawia, że są one wszechstronnym narzędziem w różnych branżach.
Jakie są najczęstsze problemy związane z destylatorami do rozpuszczalników
Podczas użytkowania destylatorów do rozpuszczalników mogą wystąpić różne problemy, które mogą wpłynąć na efektywność procesu oraz jakość uzyskiwanych produktów. Jednym z najczęstszych problemów jest nieprawidłowe ustawienie temperatury grzania, co może prowadzić do niepełnej separacji składników lub ich degradacji. W przypadku niewłaściwej temperatury wrzenia może dojść do powstawania niepożądanych produktów ubocznych, które obniżają jakość końcowego produktu. Innym problemem mogą być zatory w chłodnicy spowodowane osadami lub zanieczyszczeniami chemicznymi, co ogranicza efektywność skraplania par i prowadzi do obniżenia wydajności całego procesu. Regularne czyszczenie i konserwacja urządzenia są kluczowe dla uniknięcia tego typu problemów. Ponadto użytkownicy mogą napotkać trudności związane z kontrolą ciśnienia wewnętrznego w systemie, co może prowadzić do niebezpiecznych sytuacji oraz uszkodzeń urządzenia. Ważne jest również zapewnienie odpowiednich warunków wentylacyjnych podczas pracy z substancjami chemicznymi, aby uniknąć gromadzenia się oparów toksycznych.
Jak wybrać odpowiedni destylator do rozpuszczalników dla siebie
Wybór odpowiedniego destylatora do rozpuszczalników to kluczowy krok dla każdego użytkownika planującego rozpoczęcie pracy z tymi urządzeniami. Na początku warto określić swoje potrzeby oraz wymagania dotyczące procesu destylacji. Istotnym czynnikiem jest rodzaj substancji chemicznych, które będą przetwarzane – różne rozpuszczalniki mają różne temperatury wrzenia oraz właściwości chemiczne, co wpływa na wybór konstrukcji destylatora. Kolejnym aspektem jest wydajność urządzenia – jeśli planujesz przetwarzać duże ilości substancji, warto zainwestować w bardziej zaawansowany model kolumnowy lub przemysłowy. Należy również zwrócić uwagę na materiały użyte w budowie destylatora – stal nierdzewna czy szkło borokrzemowe powinny być preferowane ze względu na swoją odporność chemiczną i trwałość. Dobrze jest także sprawdzić dostępność części zamiennych oraz serwisu technicznego dla danego modelu – to ważne dla długotrwałego użytkowania urządzenia. Nie bez znaczenia są także opinie innych użytkowników oraz rekomendacje specjalistów w branży – warto poszukać informacji na temat konkretnych modeli przed podjęciem decyzji o zakupie.
Jakie przepisy regulują użycie destylatorów do rozpuszczalników
Użycie destylatorów do rozpuszczalników podlega różnym regulacjom prawnym oraz normom bezpieczeństwa, które mają na celu ochronę zdrowia ludzi oraz środowiska naturalnego. W wielu krajach istnieją przepisy dotyczące przechowywania i transportu substancji chemicznych, które muszą być przestrzegane przez użytkowników destylatorów. W Unii Europejskiej obowiązuje szereg dyrektyw dotyczących substancji niebezpiecznych oraz ich klasyfikacji, a także regulacje dotyczące ochrony środowiska związane z emisją oparów chemicznych podczas procesów produkcyjnych. Użytkownicy muszą również przestrzegać norm BHP związanych z obsługą urządzeń chemicznych – to obejmuje m.in. stosowanie odpowiednich środków ochrony osobistej oraz zapewnienie wentylacji w pomieszczeniach roboczych. Dodatkowo wiele krajów wymaga uzyskania specjalnych zezwoleń na prowadzenie działalności związanej z przetwarzaniem substancji chemicznych oraz ich sprzedażą.
Jakie innowacje technologiczne wpływają na rozwój destylatorów
Innowacje technologiczne mają ogromny wpływ na rozwój destylatorów do rozpuszczalników, przyczyniając się do zwiększenia ich efektywności oraz bezpieczeństwa użytkowania. W ostatnich latach obserwuje się rosnące zainteresowanie automatyzacją procesów produkcyjnych – nowoczesne destylatory często wyposażone są w zaawansowane systemy sterowania komputerowego umożliwiające precyzyjne monitorowanie parametrów pracy urządzenia. Dzięki temu użytkownicy mogą łatwo dostosować ustawienia do specyfiki przetwarzanych substancji oraz optymalizować procesy produkcyjne w czasie rzeczywistym. Innowacyjne technologie pozwalają także na lepsze zarządzanie energią – nowoczesne modele często wykorzystują systemy odzysku ciepła lub energooszczędne grzałki elektryczne, co przekłada się na niższe koszty eksploatacji urządzeń.